Poor inventory management leads to a major loss of time. Downtime can cost anything from $140,000 to $5 million per hour on average. That is enough to cripple even the most well-prepared organizations, let alone small businesses operating down the street. Here we will dive into the advantages of inventory management software, cloud-based vs. desktop, and its basic features.
Inventory Management: What Is It and How Does It Work?
Inventory management software offers organizations additional control beyond basic tracking and reordering. This leads to better demand forecasting, production, and quality. All of which contribute to higher business growth, happy clients, and better financial planning.
In today’s competitive world, where inventory moves frequently, organizations must maintain track of inventory levels. Inventory management software allows its users to view a consolidated record of every item in any facility or warehouse. Determining where these items are housed and if they are in stock would now only be a few clicks away.
When running low on essential supplies, delivery requests can now be sent to vendors automatically. This, combined with a multitude of other equally important functions, make inventory management software a must-have for your organization by taking stock of “cloud inventory”.
Track in Real-Time
Imagine running an organization with countless inventory and equipment across numerous locations. Without the advantages of cloud inventory management software, it’s difficult to keep track of everything in real-time. The inability to track in real-time could then interfere with accounting down the line.
This is why organizations have started investing in industry-standard, high-quality inventory management software that streamlines managing assets in the most straightforward and effective way possible while increasing accuracy with their accounting division.
Manual vs Automated Inventory Management
At the start, manual tracking is quite appropriate. However, as your organization and inventory expand, this becomes an increasingly significant time constraint. Additionally, it could even damage your organization’s capital if you fail to come to a resolution.
Companies are now investing more in inventory management software to tackle these challenges as well as streamline accounting. The hours wasted on manual effort previously may now be spent on productive work, credited to automation and cloud inventory.
What is Cloud Inventory Management?
Now you may be asking yourself, “What is Cloud Inventory Management?” and how does it tie in with my business?
As an example, field workers may use barcode scanners to scan and monitor equipment. That data would then be promptly updated for a manager working from home. Not only does this enhance productivity, but your clients will also appreciate accuracy as your items are supplied correctly and on time.
In the coming years, these technologies will become increasingly more critical for companies as machines continue to dominate and drive profitability and growth through innovative solutions. Machines and automation will play a significant role in the future of warehousing and businesses as they ride the wave by migrating to cloud inventory.
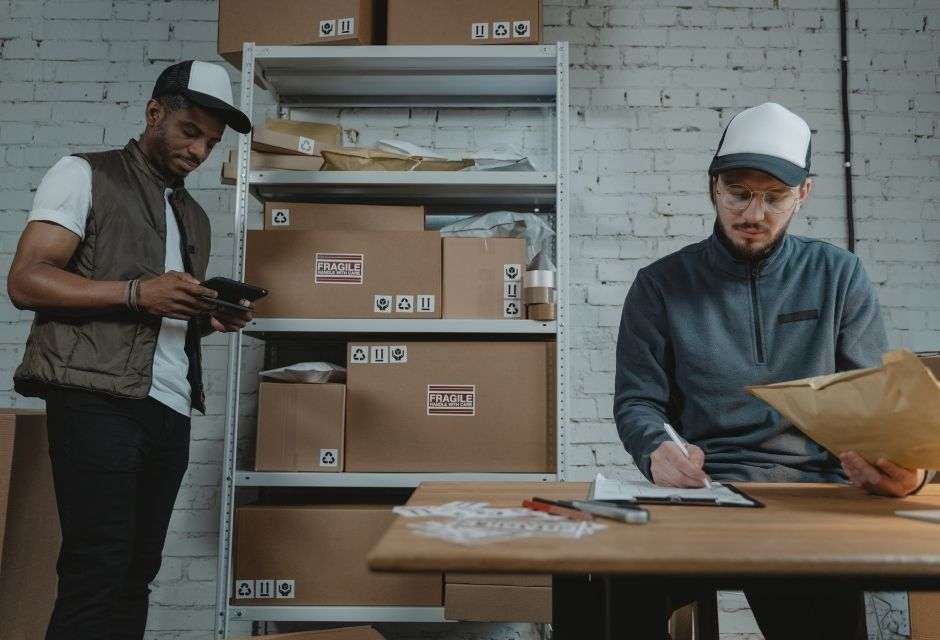
Common Capabilities
Optimization
Having too many of the same tools or not having the right tools when needed is a big problem. Inventory optimization can help you figure out how many of each item you should have, and with consolidated data from your software, you can figure out how much your assets will depreciate over time to better manage equipment life-cycle.
Alerts and Notifications
Staying alert is the best way to protect yourself. With this feature, you receive alerts when you set triggers for important matters you want the system to inform you about. You can be alerted if there aren’t enough inventory items, when an asset is overdue and hasn’t been returned on time, or when an asset is due for service again soon.
Quick Reports
There are a lot of situations where you need to send information to the government, such as the IRS, and your accounting division needs to get a report right away. Inventory management software lets you make a variety of financial and accounting reports whether you need to figure out how much maintenance summaries or fixed-asset depreciation will cost.
Data Science
Aside from the custom monthly reports, you can look back at inventory data from any point in time to see how your business has changed. Most systems use data science (data analytics) to give you useful and informative information about your business. As with having real-time, up-to-date data, having previous data is important in understanding what your business has been doing correctly, and what needs to change for better time and money management.
Management of Multiple Facilities
What if you have more than one location? To make managing inventory easier, users can sync all of their inventory data into one system. Here at SoftLedger, we like to call that our “Multi-Entity” solution. For example, one could quickly and easily consolidate all inventory and equipment data from multiple locations in real-time.
Enhance Your Inventory Management Operation
The future of inventory management software is all about using cloud inventory in order to meet your business needs. If you’re looking for a way to enhance your logistics, the best thing you can do is find an inventory management software that comes with a majority of these advantages/features as well as the ability to store cloud inventory.
Within SoftLedger’s cloud-native accounting platform and APIs is our manufacturing and inventory management software that gives users the ability to track their costs through every stage of production. For businesses where inventory is key to daily operations, tracking inventory in an organized, scalable way is absolutely critical. In order to properly manage your business, and make informed strategic decisions you must always have visibility into these items throughout their various stages of production.
SoftLedger’s flexibility and easy implementation will empower your business to always have a clear understanding of your inventory balances.
Curious to see what it can do? Watch the below intro video or book a demo with us for a full look at the platform’s capabilities.